1. Cost Analysis
a. Invest In: Weld Tooling or Piece Part Manufacturing
2. Low Tolerance Piece Parts (± 0.050” at best)
a. Saw Cutting – Minimuim
b. Press Break Forming
c. CNC Flame Cutting – Better
3. High Tolerance Piece Parts (± 0.030” or Better)
a. Laser Cutting (Low Production) – Better
b. Hard Tooling / Stamped Piece Parts (High Production) – Best
c. CNC Press Break and Tube Bending
d. Go / No-Go gauges for piece part qualifications
4. Tolerances Held on Critical Features (Before or After Welding)
a. Do tolerances of completed part require secondary machining of
piece part or completed weldment?
i. Example – Bushing Surfaces which must be free of burn through
– Bore after welding
5. Tolerances of Completed Weldment
a. Cycle time can affect tooling effectiveness
i. Allowing part to cool while clamped in tooling can control
weld pull
6. Weldment Design to Compensate for Loose Tolerance on Piece Parts
a. Other features opened up on mating parts to compensate
b. Allow uncontrolled dimensions to drift to open space
a. Invest In: Weld Tooling or Piece Part Manufacturing
2. Low Tolerance Piece Parts (± 0.050” at best)
a. Saw Cutting – Minimuim
b. Press Break Forming
c. CNC Flame Cutting – Better
3. High Tolerance Piece Parts (± 0.030” or Better)
a. Laser Cutting (Low Production) – Better
b. Hard Tooling / Stamped Piece Parts (High Production) – Best
c. CNC Press Break and Tube Bending
d. Go / No-Go gauges for piece part qualifications
4. Tolerances Held on Critical Features (Before or After Welding)
a. Do tolerances of completed part require secondary machining of
piece part or completed weldment?
i. Example – Bushing Surfaces which must be free of burn through
– Bore after welding
5. Tolerances of Completed Weldment
a. Cycle time can affect tooling effectiveness
i. Allowing part to cool while clamped in tooling can control
weld pull
6. Weldment Design to Compensate for Loose Tolerance on Piece Parts
a. Other features opened up on mating parts to compensate
b. Allow uncontrolled dimensions to drift to open space
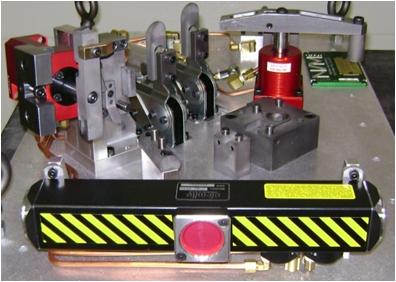